Highly selective production of renewable methyl acrylate via aldol condensation over Cu modified nitrogen-containing Beta zeolites
Abstract
Highly selective synthesis of renewable methyl acrylate from bio-sourced formaldehyde and methyl acetate through one-step aldol condensation was successfully realized on Cu-modified nitrogen-containing Beta (NBeta) catalysts. Silicon-29 magic angle spinning nuclear magnetic resonance (29Si MAS NMR), Fourier transform infrared spectroscopy (FT-IR), temperature-programmed desorption of ammonia, temperature-programmed desorption of carbon dioxide, and element analysis indicate that nitridation weakens the acid strength, reduces the number of acidic sites and introduces basic sites through the formation of Si−N bond on Beta zeolites, thereby promoting methyl acrylate selectivity and reducing the coke formation. Adding Cu into NBeta further finely tunes the basicity and acidity balance and thus inhibits the by-product acetone. High methyl acrylate selectivity of 95% and formaldehyde conversion of 99% were achieved over Cu/NBeta catalyst under optimized conditions. The coke content decreases remarkably from 28% on H-form Beta (HBeta) zeolites to 17% on NBeta zeolites doped with Cu due to its appropriate basicity/acidity. Cu/NBeta has good regeneration capability, and the weakening of Si-N species may account for the decline of catalytic performance after successive regeneration. The catalytic performance was restored when the regenerated catalyst was nitridated again.
Keywords
INTRODUCTION
As important intermediates in organic synthesis, acrylic acid and its derivatives, such as methyl acrylate, are widely used in producing adhesives, synthetic resins, and paint and coating additives[1,2]. Acrylic acid can be obtained through the two-step oxidation of propylene, of which the first step is propylene oxidation to acrolein, then further oxidation to acrylic acid[3], and esterification to methyl acrylate. This process is long and complex, and there is a risk of excessive oxidation of propylene and the required products. In addition, this route depends on the fossil resources and is not environmentally benign and sustainable. Therefore, it is essential to develop a new alternative. In recent years, the one-step preparation of methyl acrylate from methyl acetate and formaldehyde through the aldol condensation has attracted extensive attention[4-6]. This is a promising and even renewable pathway for producing methyl acrylate because both the feedstocks, formaldehyde and methyl acetate, can be derived from bio-based methanol[7].
At present, aldol condensation reactions are mainly carried out on solid catalysts, including acidic[4,8,9], basic[5,10], and acid-base bifunctional catalysts[11-13]. Solid acidic catalysts mainly include phosphates[8] and zeolites[9,14]. Khalameida et al. reported titanium phosphates for aldol condensation of acetic acid and formaldehyde with an acrylic acid selectivity of 80%[8]. Ma et al. used HZSM-35 and Cs/ZSM-35 zeolites to catalyze the aldol condensation[6,9]. They believed that the medium and weak strong acids in the catalyst benefit this reaction. Although solid acidic catalysts have fairly good catalytic performance, the selectivity of methyl acrylate is relatively low due to many side reactions caused by the strong acidic sites. Solid basic catalysts are mainly supported alkali metal/alkaline earth metal catalysts[5,10,15]. He et al. loaded Li, Na, K, Rb, and Cs on SBA-15 to catalyze the reaction of methyl acetate and formaldehyde to synthesize methyl acrylate[16]. They found that Cs/SBA-15 had the best reaction performance, and the selectivity of methyl acrylate was 91%[5]. Yan et al. also obtained the similar results on Cs/SBA-15 with methyl acrylate selectivity of 95%, but the conversion of methyl acetate was as low as 48%[17]. Although supported basic catalysts have high selectivity for methyl acrylate, they are usually unstable, prone to deactivation and difficult to regenerate. The acid-base bifunctional catalysts with balanced acidic and basic properties show good catalytic performance in aldol reaction owning to the acid-base synergistic effect[18,19]. Formaldehyde is protonated to form C+ cation on the acidic site, and methyl acetate is activated to remove α-H to form α-C- anion on the basic site. Then, the addition of the C+ cation to the α-C- anion forms an unstable intermediate aldol, and a molecule of water is removed on an acidic site to form methyl acrylate[12]. Bao et al. reported a bifunctional Ba-La/Al2O3 catalyst, the conversion of methyl acetate was ~40%, and the selectivity of methyl acrylate was ~94%[20]. Guo et al. demonstrated that the vanadium phosphorus (VP) oxide catalyst with a P/V atomic ratio of 1.2 exhibited the best activity due to the higher fraction of VOPO4 entity and (VO)2P2O7 phase with balanced acidity and basicity[21]. Zhao et al. reported that γ-Al2O3 loaded VP oxide (VPO) exhibited a conversion of 42% for formaldehyde and a selectivity of 92% for methyl acrylate[22]. VPO supported on SBA-15 and HZSM-5 also showed good performance to prepare methyl acrylate[23]. However, VPO catalyst systems are relatively complex, and many factors such as phase composition, V4+/V5+ ratio, support and promoter[24,25] affect their activity. Therefore, it is necessary to develop the simple and efficient acid-base bifunctional catalysts for aldol reaction and the relationship between acidity/basicity and activity needs to be further understood. High-temperature nitridation of zeolites in ammonia results in both acidic and basic sites on the surface[26-28], which has been applied in some acid-base catalytic reactions[29-31]. However, the preparation of methyl acrylate by aldol condensation catalyzed by nitrogen-containing zeolites has not been well studied.
In this paper, we prepared the nitrogen-containing Beta (NBeta) from H-form Beta (HBeta) zeolites through nitridation in ammonia at high temperatures, and their catalytic performance of the aldol condensation to prepare methyl acrylate was compared in detail. Addition of Cu into NBeta was employed to tune the acidity and basicity and further improved the reaction performance. The reactivity correlation with the structure and acid-base properties was revealed by X-ray diffraction (XRD), N2 adsorption, elemental analysis, silicon-29 magic angle spinning nuclear magnetic resonance (29Si MAS NMR), Fourier transform infrared spectroscopy (FT-IR), temperature-programmed desorption (TPD) of ammonia (NH3-TPD), and TPD of carbon dioxide (CO2-TPD). The regeneration capability and deactivation mechanism of the spent catalyst was also investigated.
EXPERIMENTAL
Catalyst preparation
NH4Beta zeolites (Si/Al = 19, Zeolyst) were calcinated at 550 °C in a muffle furnace to obtain HBeta. The nitridation of HBeta zeolites was performed in an NH3 flow at high temperatures. The samples obtained were denoted as NB-p, where p represents the nitridation temperature, ammonia flow rate, or nitridation time.
The supported Cu/NBeta catalysts with different Cu contents were prepared by impregnating NBeta zeolites with desired amount of Cu(NO3)2 solution and then were dried at 110 °C and calcined at 450 °C in N2 atmosphere. The Cu mass content was measured by inductively coupled plasma (ICP).
The regeneration of the spent catalyst was conducted in a flowing air atmosphere at a rate of 50 mL/min at 580 °C for 5 h. The re-nitridation of the regenerated catalyst was conducted in the same procedure as the nitridation of HBeta zeolites.
Characterizations
Powder XRD (PXRD) patterns were collected on an X-ray diffractometer (Rigaku Smartlab) using Cu Kα radiation (40 kV and 100 mA) with a scanning rate of 8°/min in the range of 2θ = 5°-50°.
N2 adsorption experiments were performed at -196 °C on Micromeritics ASAP 2460. The samples were pretreated at 300 °C for 4 h before measurements. The total specific surface areas were calculated using the Brunauer-Emmett-Teller (BET) method, and the pore volumes were calculated by N2 volume adsorbed at relative pressures close to p/p0 = 1.
Nitrogen element analysis was carried out on a Vario EL analyzer with a test temperature of 1,000 °C using oxygen and high-temperature oxidants as additives. Three parallel tests were conducted and the average value was taken.
Ultraviolet-visible (UV-vis) diffuse reflectance spectra were collected from 190-800 nm using a JACSO
29Si MAS NMR experiments were conducted on the Agilent DD2-500MHz spectrometer with a resonance frequency at 99.3 MHz using a 6 mm probehead and spinning rate of 6 kHz. The spectra were acquired with a π/4 pulse width of 2.8 μs, a recycle delay of 120 s and 200 scans. Chemical shifts were referenced to tetramethylsilane.
FT-IR experiments were performed on a Thermo Fisher Nicolet iS10 spectrometer equipped with an environmental temperature chamber (PIKE Technologies). All spectra were collected at 25 °C by accumulating 64 scans after the samples were dehydrated at 400 °C for 30 min under flowing N2 atmosphere. Nicolet OMNIC software converted the absorbance data into Kubelka-Munk format.
CO2- or NH3-TPD experiments were performed using a homemade instrument with mass spectrometry (Pfeiffer Omini-star, GSD-320) to characterize the basic and acidic sites over the catalysts, respectively. Typically, 37 mg of sample was used in each measurement. The sample was first purged with nitrogen at
Thermogravimetric (TG) measurements were conducted on an SDT-Q600H TG analyzer at a heating rate of 10 °C/min from room temperature to 800 °C in air flow.
TPO experiments were conducted on a homemade instrument. The samples were raised from 100 to 800 °C at a rate of 10 °C/min in 10% O2/N2 gas, and the signal curve of CO2 in exhaust gas was continuously detected by a mass spectrometer (Pfeiffer Omini-star, GSD-320).
Catalytic test
The formaldehyde conversion with methyl acetate was carried out in a 50 mL stainless steel autoclave. Before reaction, certain amounts of 37% formaldehyde aqueous solution, i.e., formalin, methyl acetate, and catalyst, were added into the reactor. The mixture was stirred at 1,200 ppm with a mechanical stirrer and heated to the desired reaction temperature. After reaction, the liquid products and the solid catalyst were separated by centrifugation, and a certain amount of isopropanol was added as an internal standard. The products were analyzed by a gas chromatograph (Shanghai Tianmei GC-7900) equipped with a flame ionization detector (FID) plus a HP-5 capillary column and a thermal conductivity detector (TCD) plus a packed GDX-403 column. The formaldehyde conversion and selectivity were calculated by:
where m0 is the mass of formaldehyde fed into the reactor; m is the mass of formaldehyde after reaction; MA and mby-product stand for the mass of methyl acrylate and by-product derived from formaldehyde, respectively.
The acetone derived from methyl acetate cannot be ignored in the reaction. Therefore, the selectivity of acetone was calculated, based on the consumed methyl acetate, by:
where nacetone and nMAC are the molar quantities of acetone and methyl acetate, respectively.
RESULTS AND DISCUSSION
Aldol condensation catalyzed by NBeta zeolites
As a comparison, the catalytic performance of the aldol condensation over HBeta zeolites was evaluated, and the results are shown in Figure 1. For HBeta, methyl acrylate selectivity is about 82%, and formaldehyde conversion is 90%. Still, lots of by-products were detected over HBeta zeolites. Although the acidic sites were reported to be essential to improve the aldol condensation[4,14], strong acidic sites lead to many side reactions such as olefin polymerization and cracking to increase by-product and coke contents. After nitridation, formaldehyde conversion and methyl acrylate selectivity increase to 97% and 94%, respectively, over NBeta catalyst. This indicates that nitridation can enhance the catalytic performance of aldol condensation. We also calculated the acetone selectivity in the by-products based on methyl acetate. It is 6% on NBeta zeolites, higher than HBeta zeolites. This demonstrates that although the increase of basic sites after nitridation improves the methyl acrylate selectivity, it will also form acetone due to the self-condensation of methyl acetate[32,33]. That is to say, both the acidity and basicity of the catalyst significantly influence the reaction performance. The nitridation conditions could affect the acidity and basicity balance of the catalyst. Therefore, we evaluated and optimized the reaction performance of NBeta zeolites prepared under different nitridation conditions, and the results are shown in Supplementary Figures 1-3. By adjusting the nitridation temperature and time and NH3 flow rate, it was found that NB-800 catalyst exhibited the best performance in the aldol condensation after nitridation in 65 mL/min NH3 at 800 °C for 12 h. A formaldehyde conversion of 97% and methyl acetate selectivity of 94% was achieved on NB-800 catalyst; therefore, it was selected as a potential catalyst for optimizing aldol reaction conditions.
Effect of the aldol reaction conditions
The effect of reaction temperature in the range of 300-360 °C on the aldol reaction performance was investigated over NB-800 catalyst and the results are shown in Figure 2. It can be seen that the reaction temperature greatly influences the selectivity of methyl acrylate. When the reaction temperature rises from 300 to 320 °C, the selectivity of methyl acrylate increases from 70% to 94% and that of others decreases from 23% to 3%. When the reaction temperature exceeds 320 °C, the selectivity of by-products increases, decreasing methyl acrylate selectivity. The conversion of formaldehyde is close to 100% without significant change upon reaction temperature. Given both the conversion and selectivity, the optimal reaction temperature is 320 °C. We also optimized other reaction conditions on the NB-800 catalyst for the aldol condensation [Supplementary Figures 4-6]. A formaldehyde conversion of 97% and methyl acrylate selectivity of 94% were achieved at optimal 320 °C, reaction time of 6 h, methyl acetate/formaldehyde molar ratio of 4, and catalyst mass of 0.1 g.
Effect of the acidity and basicity on the catalytic performance
It can be seen from Figure 1 that after nitridation of HBeta zeolites, both the formaldehyde conversion and the methyl acrylate selectivity are enhanced, but the acetone selectivity, a by-product produced by the self-condensation of methyl acetate, also increases. Basically, the production of by-product acetone may be due to the strong basicity of the catalyst[32,33]. In general, copper oxide is used as a mild Lewis acid site in many reactions[34]. Thus, Cu was loaded on NBeta catalyst in order to tune the acid-base balance and further improve the reaction performance. As shown in Figure 3, as Cu content increases from 1% to 4%, the acetone selectivity decreases from 6% to ~1%, and the formaldehyde conversion is nearly unchanged. However, too much Cu addition decreases the methyl acrylate selectivity. Overall, 2 wt% Cu/NB-800 exhibits the best methyl acrylate selectivity of 95%, formaldehyde conversion of 99%, and the acetone selectivity is only 1.3%. In this case, the carbon balance was calculated to be 91%. We also compared the reaction performance of 2 wt% Cu/NB-800 and 2 wt% Cu/HBeta catalysts in Supplementary Figure 7. It is found that 2 wt% Cu/NB-800 shows both higher formaldehyde conversion and methyl acrylate selectivity than
Catalyst characterization
XRD, N2 adsorption and nitrogen elemental analysis
Figure 4 shows the XRD patterns of HBeta and NB-800 zeolites with different Cu contents. It can be seen that all samples have the typical Beta zeolite structure[35]. After nitridation and loading Cu, the positions of the main diffraction peaks of the zeolites remain unchanged, and there is no diffraction peak of CuO due to its high dispersion on the surface of zeolites[36]. Nevertheless, the intensities of the diffraction peaks slightly decrease. This is possibly due to the reduced crystallinity caused by the partial collapse of the framework during nitridation at a temperature as high as 800 °C. Introducing a small amount of Cu does not alter the framework structure of NBeta zeolites while more Cu added causes the partial loss of crystallinity probably due to the stronger interaction between Cu acting as acid sites and basic sites on NBeta zeolites. The textural properties of the samples were determined by N2 adsorption-desorption isotherms in
Figure 4. XRD patterns of HBeta and NBeta zeolites with different Cu loadings. XRD: X-ray diffraction; HBeta: H-form Beta; NBeta: nitrogen-containing Beta.
BET surface areas, pore volumes and N contents of the samples studied herein
Samples | SBET (m2/g) | Vpore (cm3/g) | N content (wt%) |
HBeta | 568 | 0.29 | - |
NB-800 | 436 | 0.26 | 2.1 |
1Cu/NB-800 | 385 | 0.22 | 1.9 |
2Cu/NB-800 | 373 | 0.22 | 2.0 |
3Cu/NB-800 | 367 | 0.21 | 1.7 |
4Cu/NB-800 | 334 | 0.19 | 2.0 |
29Si MAS NMR and FT-IR spectra
The formation of different NHx species on the surface of nitrogen-containing samples can be detected by
Figure 5. (A) 29Si MAS NMR and (B) FT-IR spectra of HBeta and NBeta zeolites with different Cu loadings. 29Si MAS NMR: Silicon-29 magic angle spinning nuclear magnetic resonance; FT-IR: Fourier transform infrared spectroscopy; HBeta: H-form Beta; NBeta: nitrogen-containing Beta.
Figure 5B shows the FT-IR spectra of HBeta and NBeta with different Cu loadings. The spectrum of the parent HBeta zeolites shows bands at ~3,743 and 3,607 cm-1, which are assigned to silanols and bridging
NH3-TPD and CO2-TPD profiles
The acidity of HBeta and NBeta with different Cu loadings was investigated using the NH3-TPD technique
Figure 6. (A) NH3-TPD and (B) CO2-TPD profiles of HBeta and NBeta zeolites with different Cu loadings. TPD: Temperature-programmed desorption; HBeta: H-form Beta; NBeta: nitrogen-containing Beta.
Acidic and basic properties of HBeta and Cu/NBeta catalysts with different Cu contents
Samples | Acidic site (µmol/g) | Total acid amount (µmol/g) | Basic site (µmol/g) | Total base amount (µmol/g) | ||||
Weak | Middle | Strong | Weak | Middle | Strong | |||
HBeta | 12 | 71 | 47 | 130 | 1.9 | - | - | 1.9 |
NB-800 | 3 | - | - | 3 | 1.1 | 8.0 | 2.1 | 11.2 |
1Cu/NB-800 | 4 | 5 | - | 9 | 2.0 | 5.8 | 1.8 | 9.6 |
2Cu/NB-800 | 3 | 10 | 3 | 16 | 2.3 | 5.0 | - | 7.3 |
3Cu/NB-800 | 5 | 15 | 8 | 28 | 0.4 | 2.0 | - | 2.4 |
4Cu/NB-800 | 5 | 15 | 13 | 33 | 0.4 | 1.7 | - | 2.1 |
Figure 6B shows the basicity characterization results from CO2-TPD measurement. The number of basic sites of corresponding samples is listed in Table 2. HBeta zeolites have only one CO2 desorption peak centered at 380 °C, indicating HBeta zeolites have a few weak basic sites[45]. After nitridation, new CO2 desorption peaks centered at ~480 and ~610 °C appear, which are attributed to the medium-strength and strong basic sites. Both the amount and the strength of basic sites over NBeta increase obviously compared to HBeta. After addition of Cu, both the amount and the strength of basic sites over NBeta decrease. The strong basic sites disappear when Cu content increases to 2 wt% and the number of basic sites decreases gradually with the Cu content. This indicates that the addition of Cu mainly covers the strong basic sites, and excessive Cu addition also has a certain impact on the medium-strength basic sites.
By correlating the characterization results of NH3- and CO2-TPD with the reaction performance, we can conclude that both the acidity and basicity influence the catalytic performance. HBeta gives lower selectivity to methyl acrylate due to large amounts of other products formed over strong acidic sites. Nitridation of Beta decreases the acidic sites and increases the basic sites. Thus, NBeta shows higher selectivity to methyl acrylate than HBeta, which means that decreased acidic sites and increased basic sites could inhibit the side reactions and boost the aldol reaction. However, NBeta displays higher selectivity to acetone than HBeta, indicating that although the basic sites can boost the aldol reaction, strong basic sites are unfavorable for the whole reaction due to the formation of acetone. Adding Cu decreases both the amount and the strength of the basic sites over NBeta and thus inhibits the formation of acetone. In addition, the increase of medium-strength acidic sites with an appropriate amount after the addition of Cu is also beneficial for the aldol reaction, i.e., the activation of formaldehyde and the dehydration of the intermediate aldol to methyl acrylate. However, the selectivity to others increases over 4Cu/NBeta due to the presence of strong acidic sites. Furthermore, 2Cu/NBeta with a proper number of basic sites and acidic sites with medium strength results in ca. 95% methyl acrylate selectivity and only about 1% acetone selectivity.
TG/DTG analysis
The TG analysis results of different samples after reaction are shown in Figure 7. TG profiles in Figure 7A display two obvious weight loss peaks centered at ~380 and ~535 °C according to the derivative thermogravimetry (DTG) results in Figure 7B. Combined with the TPO measurement shown in Supplementary Figure 10, no CO2 signal is found when the temperature is lower than 200 °C, indicating that the weight-loss peak before 200 °C in Figure 7B is from water on the catalyst surface. Based on DTG and TG diagrams, the main carbon weight-loss peak on HBeta appears at about 535 °C with only a weak weight-loss peak at ~380 °C. This can be attributed to the carbon deposits formed on the strong acidic centers and weak acidic centers of the catalyst[9], respectively. For spent HBeta, the coke content reaches as high as ~28%. For NBeta after aldol reaction, the coke content decreases to 20% owing to the reduced acid strength and density on Beta zeolites. When Cu was introduced on NBeta, the coke content further decreases to ~17%. This means that a balanced acidity and basicity on 2Cu/NBeta enhanced the aldol reaction performance and reduced the by-products that may cause coke.
Successive regeneration of spent Cu/NBeta catalyst
The regeneration capability of spent catalyst is very important for its practical applications. Figure 8 shows that both formaldehyde conversion and methyl acrylate selectivity can be properly restored after three successive regeneration cycles of the 2 wt% Cu/NBeta catalyst. Formaldehyde conversion decreases from ca. 99% to 86%, and methyl acrylate selectivity decreases slightly from 95% to 90% after the fourth regeneration cycle.
Figure 8. Catalytic performance of spent 2Cu/NBeta after successive regeneration cycles. NBeta: Nitrogen-containing Beta.
The 2 wt% Cu/NBeta catalyst before and after regeneration was characterized by XRD, 29Si MAS NMR, and CO2-TPD to investigate the deactivation mechanism during regeneration by air. XRD patterns of the catalyst before and after regeneration in Supplementary Figure 11 indicate the intensities of the characteristic diffraction peaks decrease gradually after successive regeneration cycles. The intensity of the diffraction peak at 35.6° rises with the increase of the cycling numbers. This may be due to the accumulation of some unremoved coke on one of the crystal faces as the cycling numbers increase. 29Si MAS NMR was employed to characterize the local structures of the catalyst before and after regeneration [Figure 9]. The
CONCLUSIONS
In this study, the catalytic performance of the one-step condensation of bio-based formaldehyde and methyl acetate to renewable methyl acrylate was evaluated over Cu-modified NBeta catalysts. 29Si MAS NMR,
DECLARATIONS
Authors’ contributions
Carried out experiments, analyzed data, interpreted results, and wrote the draft manuscript: Wang M
Analyzed data and discussed results: Xu L
Directed and supervised the project, discussed results, and revised the manuscript: Zhang W
Availability of data and materials
Not applicable.
Financial support and sponsorship
The financial support from the National Natural Science Foundation of China (No. 21673027) was acknowledged.
Conflicts of interest
All authors declared that there are no conflicts of interest.
Ethical approval and consent to participate
Not applicable.
Consent for publication
Not applicable.
Copyright
© The Author(s) 2024.
Supplementary Materials
REFERENCES
1. Wang G, Li Z, Li C, Zhang S. Preparation of methyl acrylate from methyl acetate and methanol with mild catalysis of cobalt complex. Chem Eng J 2019;359:863-73.
2. Xu A, Wang Y, Ge H, Chen S, Li Y, Lu W. An outstanding Cr-doped catalyst for selective oxidation of propane to acrylic acid. Chin J Catal 2013;34:2183-91.
3. Fang W, Ge Q, Yu J, Xu H. Catalytic selective oxidation of propane to acrylic acid in a fixed-bed reactor with an O2-distributor. Ind Eng Chem Res 2011;50:1962-7.
4. Xie M, Ni Y, Fang X, et al. Nano-sized H-ZSM-5 zeolite catalyzes aldol condensation reaction to prepare methyl acrylate and acrylic acid. Catal Sci Technol 2022;12:5171-7.
5. He T, Qu Y, Wang J. Aldol condensation reaction of methyl acetate and formaldehyde over cesium oxide supported on silica gel: an experimental and theoretical study. Catal Lett 2019;149:373-89.
6. Ma Z, Ma X, Liu H, Zhu W, Guo X, Liu Z. One-step aldol condensation reaction of dimethoxymethane and methyl acetate over supported Cs/ZSM-35 zeolite catalysts. Chin J Catal 2018;39:1129-37.
7. Gautam P, Neha, Upadhyay S, Dubey S. Bio-methanol as a renewable fuel from waste biomass: current trends and future perspective. Fuel 2020;273:117783.
8. Khalameida S, Nebesnyi R, Pikh Z, et al. Catalytic aldol condensation of formaldehyde with acetic acid on titanium phosphates modified by different techniques. Reac Kinet Mech Cat 2018;125:807-25.
9. Ma Z, Ma X, Ni Y, et al. HZSM-35 zeolite catalyzed aldol condensation reaction to prepare acrylic acid and its ester: effect of its acidic property. Chin J Catal 2018;39:1762-9.
10. Li J, Tai J, Davis RJ. Hydrocarbon oxidation and aldol condensation over basic zeolite catalysts. Catal Today 2006;116:226-33.
11. Bao Q, Bu T, Yan J, et al. Synthesis of methyl acrylate by aldol condensation of methyl acetate with formaldehyde over Al2O3-supported barium catalyst. Catal Lett 2017;147:1540-50.
12. Zhang G, Zhang H, Yang D, Li C, Peng Z, Zhang S. Catalysts, kinetics and process optimization for the synthesis of methyl acrylate over Cs-P/γ-Al2O3. Catal Sci Technol 2016;6:6417-30.
13. Yang D, Li D, Yao H, et al. Reaction of formalin with acetic acid over vanadium-phosphorus oxide bifunctional catalyst. Ind Eng Chem Res 2015;54:6865-73.
14. Dumitriu E, Hulea V, Fechete I, Auroux A, Lacaze J, Guimon C. The aldol condensation of lower aldehydes over MFI zeolites with different acidic properties. Microporous Mesoporous Materials 2001;43:341-59.
15. Wang Y, Chen H, Zhao G, Liu M, Lang X, Zhu Z. Influence of support properties on the activity of basic catalysts for aldol condensation of formaldehyde and methyl acetate in a continuous-flow reactor. J Flow Chem 2015;5:87-94.
16. He T, Qu Y, Wang J. Experimental and theoretical study for vapor phase aldol condensation of methyl acetate and formaldehyde over alkali metal oxides supported on SBA-15. Ind Eng Chem Res 2018;57:2773-86.
17. Yan J, Zhang C, Ning C, et al. Vapor phase condensation of methyl acetate with formaldehyde to preparing methyl acrylate over cesium supported SBA-15 catalyst. J Ind Eng Chem 2015;25:344-51.
18. Zeidan R, Davis M. The effect of acid-base pairing on catalysis: an efficient acid-base functionalized catalyst for aldol condensation. J Catal 2007;247:379-82.
19. Tichit D, Lutic D, Coq B, Durand R, Teissier R. The aldol condensation of acetaldehyde and heptanal on hydrotalcite-type catalysts. J Catal 2003;219:167-75.
20. Bao Q, Zhu W, Yan J, et al. Vapor phase aldol condensation of methyl acetate with formaldehyde over a Ba-La/Al2O3 catalyst: the stabilizing role of La and effect of acid-base properties. RSC Adv 2017;7:52304-11.
21. Guo X, Yang D, Zuo C, Peng Z, Li C, Zhang S. Catalysts, process optimization, and kinetics for the production of methyl acrylate over vanadium phosphorus oxide catalysts. Ind Eng Chem Res 2017;56:5860-71.
22. Zhao H, Zuo C, Yang D, Li C, Zhang S. Effects of support for vanadium phosphorus oxide catalysts on vapor-phase aldol condensation of methyl acetate with formaldehyde. Ind Eng Chem Res 2016;55:12693-702.
23. Hu J, Lu Z, Yin H, et al. Aldol condensation of acetic acid with formaldehyde to acrylic acid over SiO2-, SBA-15-, and HZSM-5-supported V-P-O catalysts. J Ind Eng Chem 2016;40:145-51.
24. Yang D, Sararuk C, Suzuki K, Li Z, Li C. Effect of calcination temperature on the catalytic activity of VPO for aldol condensation of acetic acid and formalin. Chem Eng J 2016;300:160-8.
25. Feng X, Sun B, Yao Y, Su Q, Ji W, Au C. Renewable production of acrylic acid and its derivative: New insights into the aldol condensation route over the vanadium phosphorus oxides. J Catal 2014;314:132-41.
26. Zhang C, Xu Z, Wan K, Liu Q. Synthesis, characterization and catalytic properties of nitrogen-incorporated ZSM-5 molecular sieves with bimodal pores. Appl Catal A Gen 2004;258:55-61.
27. Lesthaeghe D, Van Speybroeck V, Marin GB, Waroquier M. DFT investigation of alkoxide vs alkylammonium formation in amine-substituted zeolites. J Phys Chem B 2005;109:7952-60.
28. Kweon S, An H, Shin C, Park MB, Min H. Nitrided Ni/N-zeolites as efficient catalysts for the dry reforming of methane. J CO2 Util 2021;46:101478.
29. Lyu J, Hu H, Rui J, et al. Nitridation: A simple way to improve the catalytic performance of hierarchical porous ZSM-5 in benzene alkylation with methanol. Chin Chem Lett 2017;28:482-6.
30. Wang T, Wu G, Guan N, Li L. Nitridation of MgO-loaded MCM-41 and its beneficial applications in base-catalyzed reactions. Microporous Mesoporous Mater 2012;148:184-90.
31. Liu Y, Xu L, Zhang W. Formaldehyde and isobutene condensation via Prins reaction on HY zeolites treated with NH3. Fine Chem 2020;37:2069-75. (in Chinese) Available from: https://link.cnki.net/doi/10.13550/j.jxhg.20200332. [Last accessed on 16 Apr 2024]
32. Boekaerts B, Sels BF. Catalytic advancements in carboxylic acid ketonization and its perspectives on biomass valorisation. Appl Catal B Environ 2021;283:119607.
33. Mekhemer GAH, Halawy SA, Mohamed MA, Zaki MI. Ketonization of acetic acid vapour over polycrystalline magnesia: in situ Fourier transform infrared spectroscopy and kinetic studies. J Catal 2005;230:109-22.
34. Xu L, Liu S, Meng X, et al. A novel tandem route to renewable isoprene over Mo-Fe oxide and mesoporous Cu/MgO composite catalysts. Appl Catal B Environ 2024;341:123341.
35. Xu L, Zhao R, Zhang W. One-step high-yield production of renewable propene from bioethanol over composite ZnCeOx oxide and HBeta zeolite with balanced Brönsted/Lewis acidity. Appl Catal B Environ 2020;279:119389.
36. Sagar GV, Rao PV, Srikanth CS, Chary KV. Dispersion and reactivity of copper catalysts supported on Al2O3-ZrO2. J Phys Chem B 2006;110:13881-8.
37. He LH, Li JJ, Han SY, et al. Dynamic evolution of HZSM-5 zeolite framework under steam treatment. Chem Synth 2024;4:1.
38. Zhao R, Xu L, Huang S, Zhang W. Highly selective production of renewable p-xylene from bio-based 2,5-dimethylfuran and ethylene over Al-modified H-Beta zeolites. Catal Sci Technol 2019;9:5676-85.
39. Dogan F, Hammond KD, Tompsett GA, et al. Searching for microporous, strongly basic catalysts: experimental and calculated 29Si NMR spectra of heavily nitrogen-doped Y zeolites. J Am Chem Soc 2009;131:11062-79.
40. Narasimharao K, Hartmann M, Thiel HH, Ernst S. Novel solid basic catalysts by nitridation of zeolite beta at low temperature. Microporous Mesoporous Mater 2006;90:377-83.
41. Kawano A, Moteki T, Ogura M. Effect of delamination on active base site formation over nitrided MWW-type zeolite for Knoevenagel condensation. Microporous Mesoporous Mater 2020;299:110104.
42. Shutilov RA, Zenkovets GA, Paukshtis EA, Gavrilov VY. Localization of the copper-containing component in the pore volume of zeolite ZSM-5. Kinet Catal 2014;55:243-51.
43. Khallouk K, Solhy A, Idrissi N, Flaud V, Kherbeche A, Barakat A. Microwave-assisted selective oxidation of sugars to carboxylic acids derivatives in water over zinc-vanadium mixed oxide. Chem Eng J 2020;385:123914.
44. Wu G, Guan N, Li L. Recent development of nitrogen-incorporated molecular sieves. Chin J Catal 2012;33:51-9. (in Chinese) Available from: https://guan.nankai.edu.cn/_upload/article/files/36/25/0754df344c98aa75e4d1d1632b97/da5cafcc-5073-4f51-82ad-74c148c43938.pdf. [Last accessed on 16 Apr 2024]
Cite This Article
Export citation file: BibTeX | RIS
OAE Style
Wang M, Xu L, Zhang W. Highly selective production of renewable methyl acrylate via aldol condensation over Cu modified nitrogen-containing Beta zeolites. Chem Synth 2024;4:24. http://dx.doi.org/10.20517/cs.2024.04
AMA Style
Wang M, Xu L, Zhang W. Highly selective production of renewable methyl acrylate via aldol condensation over Cu modified nitrogen-containing Beta zeolites. Chemical Synthesis. 2024; 4(2): 24. http://dx.doi.org/10.20517/cs.2024.04
Chicago/Turabian Style
Wang, Mei, Lulu Xu, Weiping Zhang. 2024. "Highly selective production of renewable methyl acrylate via aldol condensation over Cu modified nitrogen-containing Beta zeolites" Chemical Synthesis. 4, no.2: 24. http://dx.doi.org/10.20517/cs.2024.04
ACS Style
Wang, M.; Xu L.; Zhang W. Highly selective production of renewable methyl acrylate via aldol condensation over Cu modified nitrogen-containing Beta zeolites. Chem. Synth. 2024, 4, 24. http://dx.doi.org/10.20517/cs.2024.04
About This Article
Special Issue
Copyright
Data & Comments
Data
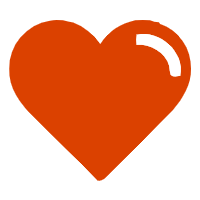

Comments
Comments must be written in English. Spam, offensive content, impersonation, and private information will not be permitted. If any comment is reported and identified as inappropriate content by OAE staff, the comment will be removed without notice. If you have any queries or need any help, please contact us at support@oaepublish.com.