Proton exchange membrane fuel cells: application for value-added chemical productions
Abstract
Proton exchange membrane fuel cells (PEMFCs) can be used as reactors to produce chemicals and co-generate electricity and chemicals. Their mild reaction conditions, high product selectivity, and energy utilization have profoundly impacted gas separation, water treatment, and energy utilization fields. Given the lack of systematic reports on the current research status of utilizing PEMFCs for chemical production and the co-production of electricity and chemicals, this article summarizes the types of reactions and catalyst usage involved in this multifaceted application. It analyzes how to improve the production and performance of the system from four aspects: electrolyte membranes, catalysts, assembly methods, and reaction processes. Finally, the article analyzes the current research shortcomings in utilizing PEMFCs for these applications and provides prospects for future development.
Keywords
INTRODUCTION
Fuel cells are green and efficient power generation devices, representing the fourth generation of power generation technology after hydropower, thermal, and nuclear power. Many developed countries and developing nations worldwide have elevated fuel cell development to a national strategic level, particularly in the field of transportation applications[1]. Among them, the proton exchange membrane fuel cells (PEMFCs) have been widely used in portable power sources, transportation sectors, etc. Moreover, research and development of hydrogen fuel PEMFCs for automobiles have become even more vigorous than before[1,2]. With the development of science and technology, researchers have expanded fuel cell reactors to produce high-value-added chemicals. Using fuel cell methods to create chemicals with fuel cells offers several advantages over traditional catalytic methods. For instance, the isolation of different reactants enhances system safety; continuous circulation of reactants at the electrodes improves catalytic performance and the ease of product separation from reactants. Furthermore, the integration of fuel cells for the simultaneous production of chemicals and electrical energy has shown strong potential for various applications. Their capability to simultaneously generate power, produce chemicals, and contribute to environmental protection profoundly influences energy utilization[3,4]. Solid oxide fuel cells (SOFCs) have garnered significant research attention due to their high operating temperature, which enables reduced impurity presence and the utilization of non-precious metal catalysts with superior catalytic performance. Numerous studies have reported the simultaneous production of electrical energy and chemicals using SOFCs[5,6]. However, it is challenging to use them at operating temperatures < 600 °C. The cost and stability issues of catalysts hinder the application of SOFCs for chemical production and the co-production of electricity and chemicals. On the other hand, the PEMFCs can operate at relatively low temperatures (low temperature ~70-95 °C, high temperature ~120-250 °C), with lower operational costs and faster response times, providing the possibility to achieve chemical production and the co-production of electricity and chemicals at lower operating costs. Currently, researchers have summarized their applications in the production of chemicals and the co-generation of electricity and chemicals[7-9]. However, existing review articles either focus on fuel cell reactions with a specific fuel or provide a general overview of the production of chemicals or the co-generation of electricity and chemicals using PEMFCs. Therefore, it is necessary to publish a comprehensive review article to summarize the current research status in this field. This article attempts to collect and summarize previous research on utilizing PEMFCs to obtain chemicals or simultaneously produce electrical energy and chemicals. It analyzes the types of feasible reactions and the catalysts involved, summarizes the ways to enhance the capacity and performance of PEMFCs, and provides a future outlook on the development of PEMFCs in co-generation energy and chemical products.
FUNDAMENTAL OF PEMFCS FOR CHEMICAL PRODUCTIONS
PEMFCs, a commonly used form of fuel cells, offer advantages such as high power density, low operating temperature, and minimal noise. Reactors also possess the benefits of mild reaction conditions and high product selectivity. Based on different operating temperatures, PEMFCs can be classified into low-temperature (~70-95 °C) PEMFCs (recorded as LT-PEMFCs) and high-temperature (~120-250 °C) PEMFCs (recorded as HT-PEMFCs). Compared to LT-PEMFCs, HT-PEMFCs have attracted increasing attention due to their improved reaction kinetics on the electrodes, enhanced tolerance to fuel/air impurities, simplified stack design, and better thermal and water management[1]. Generally, a single cell of PEMFCs consists of an anode gas diffusion layer, an anode catalyst layer, a proton exchange membrane, a cathode catalyst layer, a cathode gas diffusion layer, and bipolar plates [Figure 1]. The proton exchange membrane separates the two electrodes. Hydrogen gas undergoes an oxidation reaction to produce protons in the anode catalyst layer. It reacts with oxygen in the cathode catalyst layer through the proton exchange membrane, generating internal current. The electron flow isolated by the proton exchange membrane passes through the external circuit to produce electricity. Utilizing PEMFCs as reactors for synthesizing value-added chemicals, dehydrogenation reactions (partial oxidation) can occur at the anode, and gases that can be oxidized, such as hydrogen, methanol, and methane, can be used as fuel gases. Hydrogenation reactions can occur at the cathode, and substances with oxidation ability, such as oxygen, carbon dioxide, and cyclic ketones, can be used at the cathode. If the overall fuel cell has a positive standard free enthalpies change, the partial external voltage is required to drive the reactions [Figure 1A and B]. If the standard free enthalpies change is negative, co-generation of electricity and chemicals can be achieved [Figure 1C and D].
REACTION TYPES AND CATALYSTS OF PEMFCS FOR CHEMICAL PRODUCTIONS
Considering the operating temperature of PEMFCs, the chemical reactions that can be achieved on PEMFCs mainly involve reactions that can be carried out at relatively low temperatures (below 250 °C). Currently, the responses that can be realized at the anode as reactors include methanol/ethanol oxidation, methane oxidation, and propene epoxidation. In contrast, the reactions achieved at the cathode mainly include CO2 reduction, H2O2 production, and hydrogenation of some alkynes or cyclic ketones. However, to the best of our knowledge, there is no report of producing high value-added chemicals in the cathode and anode simultaneously. Table 1 summarizes the current research on chemical production using PEMFCs and shows that both the cathode and anode reactions predominantly utilize precious metal catalysts (Pt or Pd) with carbon materials as the support. The selectivity of the product is high, but the yield is low.
Selected research on the utilization of PEMFCs for chemical production
Section | Reactions | Catalyst | Conv. | Current density | Main product | Ref. |
Anode | 2CH3OH → HCOOCH3 + 4H+ + 4e- | Pt-Ru/C | - | 50 mA/cm2 at 1.7 V (vs. SHE) | HCOOCH3 [7-9 μmol/(min·cm2)] FE (80%) | [10] |
CH2CH3OH + H2O → CH3COOH + 4H+ + 4e- | PtRu/C 2:1 | - | 740 mA/cm2 | CH3COOH FE (15%) | [11] | |
3CH3CH2OH → CH3CH(OCH2CH3)2 + H2 + H2O | Pt/C | - | ~20 mA/cm2 at 2.0 V (vs. SHE) | CH3CH(OCH2CH3)2 FE (78%) | [12] | |
CH3CH2OH → CH3CHO + 2H+ + 2e- | PtRu/C | 1% | 0.2 A | CH3CHO FE (100%) | [13] | |
CH4 + H2O → CH3OH + 2H+ + 2e- | V2O5/SnO2 | - | - | CH3OH (0.03) FE (88.4%) | [14] | |
C3H6 + H2O → C3H6O (PO) + 2H+ + 2e- | PtOx(O2) | 0.4% | 13.4 mA/cm2 at 1.6 V (vs. SHE) | C3H6O [37 μmol/(h·cm2)] FE (7.4%) | [15] | |
O2 + H2 → H2O2 C3H8 + H2O2 → C2H8O + C3H6O + 7C3H6O2 | MIL-53 (Al, Fe)/C acid | ~-35 mA/cm2 at -0.2 V (vs. RHE) | C3 [2.65 μmol/(h·cm2)] | [16] | ||
CH3OH → HCHO + 2H+ + 2e- | Pd/C | - | ~50 mA/cm2 at 2.0 V | HCHO [682 mmol/(h·gcat)] FE (~45%) | [17] | |
CH3CH2OH → CH3CHO + 2H+ + 2e- | Pt-Ni/GNPs | 590 mA/cm2 at 1.4 V | CH3CHO | [18] | ||
C3H7OH → C2H5CHO + 2e- + 2H+ C2H5CHO + 2C3H7OH ⇄ C3H6 (OC3H7)2 + H2O | Pt/C | ~10 mA/cm2 at 2 V | 1,1-dipropoxypropane FE (78%) | [19] | ||
PhCH2OH → PhCHO + 2e- + 2H+ | Nafion ionomer | 8.3 mA/cm2 at 2.5 V | PhCHO FE (80%-90%) | [20] | ||
Cathode | O2 + 2H+ + 2e- → H2O2 | VGCF-XC72 | - | - | H2O2 (7%) FE (95%) | [21] |
xCO2 + 2(2x – z + y/2)H+ + 2(2x – z + y/2)e- → CxHyOz + (2x – z)H2O (CO2 reduction) | Cu-CNF | < 2% | 0.8 mA/cm2 | Acetaldehyde (85%) | [22] | |
Sn nanoparticles (60-80 nm) + 5% CNT | - | 140 mA/cm2 at 3.5 V | HCOOH (5-20 wt%) FE (94%) | [23] | ||
2.5%Cu complex/carbon Vulcan | - | 0.021 pA at -1.2 V | CH3OH [4 mol /(h·L)] FE (22%) | [24] | ||
CH3-C6H5 + 6H+ + 6e- → CH3-C6H11 | Ru/BP3500 | - | 50 mA/cm2 at -0.255 V (vs. SHE) | Methylcyclohexane FE (91%) | [25] | |
Ru(5)-Ir(5)/KB | 200 mA/cm2 at -0.183 V (vs. SHE) | Methylcyclohexane FE (86%) | [26] | |||
C14H10 + 2H+ + 2e- → C14H12 | Pt1Pd99 | 20 mA/cm2 at 0.05 V (vs. RHE) | C14H12 | [27] | ||
Pt1Pd99 | 15 mA/cm2 at 0 V (vs. RHE) | C14H12 FE (40%) | [28] | |||
C7H6O2 + 6H+ + 6e- → C7H12O2 | Pt1Ru1.5 | 3.0 mA/cm2 | C7H12O2 FE (93%) | [29] | ||
C6H8O + 2H+ + 2e- → C6H10O | Pd/C | 82% | 50 mA/cm2 | C6H10O (64%) FE (97%) | [30] | |
cyclohexanone + 2H+ + 2e- → cyclohexanol | Rh/C | 24 mA/cm2 | Cis-cyclohexanol FE (96%) | [31] |
REACTION TYPES AND CATALYSTS OF PEMFCS FOR POWER AND CHEMICALS CO-GENERATION
There are few reports on using PEMFCs for the co-generation of electricity and chemicals. The reactions involved mainly include the reduction of nitrobenzene, oxidation of phenol to benzoquinone, and production of H2O2. Table 2 summarizes the research status of utilizing PEMFCs for co-generating electricity and chemicals. Table 2 shows that the current reaction temperatures are relatively low (below 100 °C), the catalysts used are mostly carbon-supported noble metal-based catalysts, the generated electrical power is low, and the chemical yields are not high.
Selected research on the utilization of PEMFCs for co-generation of electrical energy and chemicals
Anode (catalyst) | Cathode (catalyst) | T (°C) | Chemicals | Power (mW/cm2) | Ref. |
H2 (Pt/C) | H2O2 + CH4 (Pt/C) | 80 | Methanol, formic acid and formaldehyde | 70 | [32] |
H2O + CH4 (Pd50Ni50/Sb2O5·SnO2) | O2 + H2O (Pt/C) | 85 | CH3COOH [~6.3 μmol/(h·L)] | ~0.375 | [33] |
H2 (Pt/C) | O2 + H2O (Pt/Co-C) | 60 | H2O2 [8 μmol/(h·cm2)] | 133 | [34] |
H2 (Pt/C) | Nitrobenzene (Pt/C) | 70 | Aniline FE (28.2%) | 1.5 | [35] |
Phenol (PtRu/C) | O2 (Pt/C) | 80 | Hydroquinone FE (80%) | - | [36] |
STRATEGIES TO IMPROVE PRODUCTIVITY PERFORMANCE IN PEMFCS
The components involved in PEMFCs and the reaction processes affect chemical production and electricity generation. Moreover, although the conversion rate is an important parameter for chemical production, our research has found that there are few reports mentioning conversion rates in the use of PEMFCs for chemical preparation [Table 1]. This may be related to the frequently lower conversion rates of electrochemical production of chemicals. It is well known that conversion rates are related to reaction conditions such as gas velocity, pressure, etc. However, except for one report proposing that continuous operation modes can improve the conversion rate of raw materials[30], no other research has been found on enhancing this aspect. Therefore, this section summarizes strategies to enhance the capacity and performance (mainly selectivity) of PEMFCs based on four aspects: electrolyte membranes, catalysts, assembly modes, and reaction processes.
ELECTROLYTE MEMBRANE
Polymer electrolyte membranes (PEM) are essential components of PEMFCs, which require characteristics such as high proton conductivity, mechanical stability, etc.[37] [Figure 2]. Most commercialized naphthol membranes, such as Nafion 117, are used at low temperatures (< 120 °C), while polybenzimidazole (PBI)-based membranes are preferred at higher operating temperatures. Compared to low-temperature membranes, developing membrane materials that can be used at higher temperatures can enhance the system’s tolerance to pollutants, reduce the use of precious metal catalysts, and simplify the system by eliminating the need for liquid water operation. The types of high-temperature membranes currently developed and their proton conductivities are shown in Table 3[38]. Currently, the PEMs used in the production of chemicals using PEMFCs and in chemical production and chemicals and electricity co-generation systems are mostly commercial Nafion membranes; research on the involved membrane materials and their modification are relatively lacking. In addition, recent studies have found that ionomer content in Naphthol membranes in PEMFCs affects catalytic activity. Abdelnasser et al. reported that adding Nafion ionomer could expand the electrochemical active site, accelerating the electrochemical reaction in the proton transfer process[20]. In addition to the amount, the type and properties of ionomer binders can also affect the performance of PEMFCs in electricity generation[39,40], but no related reports have been found in the production of chemicals and the co-generation of chemicals and electricity using PEMFCs.
Membrane proton conductivity for HT-PEMs
Membrane type | Proton conductivity/(mS·cm-1) |
Cesium dihydrogen phosphate solid acid | 410 |
Lonic liquid-doped membrane composites | 59-148 |
Pyridine-based PBI | 200 |
Sn0.9In0.1P2O7 | 195 |
Nanocomposite membranes (based on PBI and porous SiO2 NPs) | 244 |
Lonically cross-linked PBl-blend membranes mixed with PBI and sulfonated or phosphonated acidic polymers | 100 |
3,5-Pyridine-PBI | 279.38 |
Protic ionic liquid-modified silica | 238.17 |
Functionalized PBI | 152.41 |
H3PO4-PBI (20.4 mol per repeating unit) | 200 |
H3PO4-PTFE/PBI (300% mol) | 300 |
PBI-OO | 98 |
c-PBI-30 | 198 |
AA-MCM-41 | 356 |
PES-PVP/PTFE | 260 |
PA/PBI/SiO2 | 41 |
CATALYST
In catalyst design, because high-value-added chemicals are in a semi-stable state, controlling the degree of oxidation-reduction catalysis is necessary to produce high-value-added chemicals. As the fuel cannot be completely oxidized or reduced, some power will be lost when electricity is produced in co-generation with fuel. The current research on catalysts mainly focuses on the rational design of supports and active sites. The catalysts used mainly consist of noble metals. Researchers such as Rodríguez-Gómez et al., Kuramochi et al., Serrano-Jiménez et al, Inami et al., Nogami et al., and Fukazawa et al. have made significant contributions in the field of catalyst design and mechanism exploration[11,13,17,18,25,26,28,29]. The catalytic performance can be improved by constructing the alloy structure, changing the electronegativity of the original active atoms, and dispersing the active centers [Figure 3][28,29]. Adequate combinations of non-precious metal oxides can also achieve good catalytic performance. Lee et al. used V2O5/SnO2 as the anode catalyst to convert methane to methanol (selectivity 88.4%)[14]. Different methods of noble metal treatment may also lead to excellent catalytic performance[41]. In addition, suitable supports need to possess a large specific surface area, excellent electronic conductivity, better durability, reliable interfacial adhesion, and appropriate porosity[42]. Therefore, the current focus is on improving catalytic performance through modification of carbon supports and selecting appropriate carbon supports (such as biochar)[25,43].
Figure 3. (A) Conceptual diagram of the reaction model for the electrocatalytic semihydrogenation of alkyne to (Z)-alkene on a Pt-Pd electrocatalyst. This figure is quoted with permission from Nogami et al.[28]; (B) Proposed mechanism for the electrocatalytic hydrogenation of BA using a PtRu catalyst in a PEM rector. This figure is quoted with permission from Fukazawa et al.[29]. BA: Benzoic acids; PEM: polymer electrolyte membranes.
ASSEMBLY METHOD
Currently, there are three main methods for assembling membrane electrodes: the catalyst layer loaded on the gas diffusion layer (CCS), the catalyst layer loaded on the proton exchange membrane (CCM), and the catalyst layer loaded on the proton exchange membrane through transfer (DTM) [Figure 4]. The advantages and disadvantages of these three assembly methods are shown in Table 4[44]. Compared to the demanding technical requirements of the DMT method and the significant mass transfer resistance caused by the CCS approach, the CCM method can achieve excellent catalytic performance at a higher cost-effectiveness[44]. Rodríguez-Gómez et al. achieved higher catalytic performance in ethanol oxidation for acetic acid production by loading the catalyst layer on the proton exchange membrane and using carbon paper as the gas diffusion layer[45]. The assembly method can improve mass transfer and other issues in the reaction system, thus affecting catalytic performance. However, currently, there is insufficient research on the impact of assembly methods on the production of chemicals and chemical-electro-thermal co-generation systems using PEMFCs, alongside a lack of studies on the kinetics aspect.
Figure 4. Three major approaches for the catalyst layer fabrication. This figure is quoted with permission from Zhao et al.[44]. CCM: The catalyst layer loaded on the proton exchange membrane; CCS: the catalyst layer loaded on the gas diffusion layer; CL: catalyst layer; DTM: the catalyst layer loaded on the proton exchange membrane through transfer; GDL: gas diffusion layer; MEA: membrane electrode assembly.
Advantages and disadvantages of assembly methods
Assembly method | Advantages | Disadvantages |
CCS | Easy implementation | Catalyst inks easily penetrate GDLs |
CCM | Excellent interfacial properties between the catalyst layer and membrane | Solvent easily causes membrane expansion, and the manufacturing system is more complex than CCS |
DTM | Excellent interfacial properties between the catalyst layer and membrane, reduced membrane expansion, multilayer catalyst stack | High-cost manufacturing system, limitations on the amount of catalyst |
REACTION PROCESS
Exploration of reaction conditions, such as reaction medium, reactant concentration, and reaction temperature, can lead to efficient catalytic performance. Currently, research in the production of chemicals and chemical-electrical co-generation systems using PEMFCs mainly focuses on the influence of reactant concentration. Kishi et al. investigated the influence of water on electrolysis of reactants in multiple reaction types[10,12,17,19,25]. However, there remains a gap in understanding regarding the influence of other reaction conditions, especially the electrolyte. Although the impact of the type of electrolyte has been preliminarily explored[46], parameters such as pH, which have a significant impact on electrocatalytic performance[47], have not been fully investigated. In the oxidation reaction of alcohols, researchers have found that increasing the concentration of alcohols favors the production of high-value chemicals; adjusting the concentration can also modulate the selectivity of products [Figure 5][10,19,48]. As shown in Table 2, the preferred temperature for co-production of chemicals and electricity is around 80 °C, indicating that an appropriate operating temperature can enhance gas diffusion capability and maintain high ionic conductivity, thereby improving performance. Furthermore, in terms of the operational mode of the system, continuous operation modes, compared to batch mode, can not only reduce the consumption of raw materials but also improve the conversion rate of raw materials[30].
Figure 5. (A) Effect of 1-PrOH content on catalytic performance. This figure is quoted with permission from Abdelnasser et al.[19]; (B) Effect of MeOH content on catalytic performance. This figure is quoted with permission from Kishi et al.[10]; (C and D) Effect of EtOH content on catalytic performance . This figure is quoted with permission from Rodríguez-Gómez et al.[48]; (E and F) The operational mode of the system. This figure is quoted with permission from Mitsudo et al.[30]. AA: Acetic acid; AAL: acetaldehyde; DPP: 1,1-dipropoxypropane; EA: ethyl acetate; FE: faradaic efficiency; MF: methyl formate.
CONCLUSION AND OUTLOOK
Currently, PEMFCs can be used to produce chemicals, such as ethanol, epoxypropane, formate acid, etc., and achieve co-production of hydrogen peroxide (or formate acid, ethanol, etc.) and electricity. The catalysts used during this process are mainly carbon-supported noble metal-based catalysts, with limited reports on non-noble metal-related catalysts. Additionally, improvements in production and performance can be achieved by modifying the membrane properties and monomer usage, constructing catalyst alloy structures, utilizing the MCC membrane electrode assembly method, and studying suitable process conditions. Although significant progress has been made in utilizing PEMFCs for the production of chemicals or co-production of chemicals and electricity, the following issues still exist: (1) a restricted range of catalytic reactions involved; (2) a limited variety of catalysts and high cost, primarily focused on precious metal catalysts; (3) lower conversion rates, yields, selectivity towards single products, and current densities; (4) insufficient research on reaction intermediates and reaction pathways; (5) a lack of standardization of reaction devices and studies on the impact of the reaction process. Therefore, addressing the aforementioned issues, developing more reaction types, reducing the usage of precious metals in catalysts or exploring non-noble metal catalysts with higher cost-effectiveness, conducting comprehensive and in-depth studies on improving productivity performance, and utilizing density functional theory (DFT) and Operando characterization techniques to study reaction mechanisms are the main directions for future research.
DECLARATIONS
Authors’ contribution
Prepared and revised the manuscript: Jiang X, Chen R
Designed and revised the manuscript: Chen YX, Lu CZ
All authors contributed to the discussion and preparation of the manuscript.
Availability of data and materials
Not applicable.
Financial support and sponsorship
Authors are thankful for the financial support of the Natural Science Foundation of Fujian Province (2023H0046), the XMIREM autonomously deployment project (2023CX10, 2023GG01), the National Natural Science Foundation of China (22275185), the Major Research Project of Xiamen (3502Z20191015), the Fujian Science & Technology Innovation Laboratory for Optoelectronic Information of China (2021ZR132, 2021ZZ115).
Conflicts of interest
All authors declared that there are no conflicts of interest.
Ethical approval and consent to participate
Not applicable.
Consent for publication
Not applicable.
Copyright
© The Author(s) 2024.
REFERENCES
1. Haider R, Wen Y, Ma ZF, et al. High temperature proton exchange membrane fuel cells: progress in advanced materials and key technologies. Chem Soc Rev 2021;50:1138-87.
2. Wee JH. Applications of proton exchange membrane fuel cell systems. Renew Sustain Energy Rev 2007;11:1720-38.
3. Pan Z, Chen R, An L, Li Y. Alkaline anion exchange membrane fuel cells for cogeneration of electricity and valuable chemicals. J Power Sources 2017;365:430-45.
4. Si F, Liu S, Liang Y, Fu XZ, Zhang J, Luo JL. Fuel cell reactors for the clean cogeneration of electrical energy and value-added chemicals. Electrochem Energy Rev 2022;5:25.
5. Liu S, Liu Q, Fu XZ, Luo JL. Cogeneration of ethylene and energy in protonic fuel cell with an efficient and stable anode anchored with in-situ exsolved functional metal nanoparticles. Appl Catal B Environ 2018;220:283-9.
6. Antolini E. Low molecular weight alkane-fed solid oxide fuel cells for power and chemicals cogeneration. J Energy Chem 2023;80:711-35.
7. Alcaide F, Cabot PL, Brillas E. Fuel cells for chemicals and energy cogeneration. J Power Sources 2006;153:47-60.
8. Heng Z, Yuan X, Yin Y, Ma Z. Fuel cells reactor for chemicals and electric energy cogeneration. J Electrochem 2018;24:615-27.
9. de Souza RFB, Florio DZ, Antolini E, Neto AO. Partial methane oxidation in fuel cell-type reactors for co-generation of energy and chemicals: a short review. Catalysts 2022;12:217.
10. Kishi R, Ogihara H, Yoshida-Hirahara M, Shibanuma K, Yamanaka I, Kurokawa H. Green synthesis of methyl formate via electrolysis of pure methanol. ACS Sustain Chem Eng 2020;8:11532-40.
11. Rodríguez-Gómez A, Dorado F, de Lucas-consuegra A, de la Osa AR. Influence of Pt/Ru anodic ratio on the valorization of ethanol by PEM electrocatalytic reforming towards value-added products. J Energy Chem 2021;56:264-75.
12. Kawaguchi D, Ogihara H, Kurokawa H. Upgrading of ethanol to 1,1-diethoxyethane by proton-exchange membrane electrolysis. ChemSusChem 2021;14:4431-8.
13. Rodríguez-gómez A, Dorado F, Sánchez P, de la Osa AR. Boosting hydrogen and chemicals production through ethanol electro-reforming on Pt-transition metal anodes. J Energy Chem 2022;70:394-406.
14. Lee B, Hibino T. Efficient and selective formation of methanol from methane in a fuel cell-type reactor. J Catal 2011;279:233-40.
15. Iguchi S, Kataoka M, Hoshino R, Yamanaka I. Direct epoxidation of propylene with water at a PtOx anode using a solid-polymer-electrolyte electrolysis cell. Catal Sci Technol 2022;12:469-73.
16. Yang CH, Liu XC, Li Y, et al. Selective conversion of propane by electrothermal catalysis in proton exchange membrane fuel cell. ChemSusChem 2023:e202300699.
17. Kuramochi N, Yoshida-hirahara M, Ogihara H, Kurokawa H. Proton exchange membrane electrolysis of methanol for simultaneously synthesizing formaldehyde and hydrogen. Sustain Energy Fuels 2023;7:778-85.
18. Serrano-jiménez J, de la Osa A, Rodríguez-gómez A, Sánchez P, Romero A, de Lucas-consuegra A. Graphene-like materials as an alternative to carbon Vulcan support for the electrochemical reforming of ethanol: towards a complete optimization of the anodic catalyst. J Electroanal Chem 2022;921:116680.
19. Abdelnasser S, Hakamata T, Ogihara H, Kurokawa H. Electrochemical oxidation of 1-propanol through proton exchange membrane electrolysis. J Electroanal Chem 2023;928:117009.
20. Abdelnasser S, Matsushita H, Kurokawa H, Ogihara H. Effect of nafion ionomer on proton exchange membrane electrolysis of benzyl alcohol. Chem Lett 2023;52:560-3.
21. Yi Y, Wang L, Li G, Guo H. A review on research progress in the direct synthesis of hydrogen peroxide from hydrogen and oxygen: noble-metal catalytic method, fuel-cell method and plasma method. Catal Sci Technol 2016;6:1593-610.
22. Gutiérrez-guerra N, Valverde J, Romero A, Serrano-ruiz J, de Lucas-consuegra A. Electrocatalytic conversion of CO2 to added-value chemicals in a high-temperature proton-exchange membrane reactor. Electrochem Commun 2017;81:128-31.
23. Ju HK, Kaur G, Kulkarni AP, Giddey S. Challenges and trends in developing technology for electrochemically reducing CO2 in solid polymer electrolyte membrane reactors. J CO2 Util 2019;32:178-86.
24. Garcia LMS, Filho NGP, Chair K, et al. Methanol electrosynthesis from CO2 reduction reaction in polymer electrolyte reactors - fuel cell type using [6,6′-(2,2′-bipyridine-6,6′-diyl)bis(1,3,5-triazine-2,4-diamine)] (dinitrate-O) copper (II) complex. Mater Today Sustain 2022;19:100177.
25. Inami Y, Ogihara H, Yamanaka I. Effects of carbon supports on Ru electrocatalysis for the electrohydrogenation of toluene to methylcyclohexane. Electrocatalysis 2018;9:204-11.
26. Inami Y, Ogihara H, Nagamatsu S, Asakura K, Yamanaka I. Synergy of Ru and Ir in the electrohydrogenation of toluene to methylcyclohexane on a ketjenblack-supported Ru-Ir alloy cathode. ACS Catal 2019;9:2448-57.
27. Nogami S, Nagasawa K, Fukazawa A, Tanaka K, Mitsushima S, Atobe M. Highly selective and efficient electrocatalytic semihydrogenation of diphenylacetylene in a PEM reactor with Pt-Pd alloy cathode catalysts. J Electrochem Soc 2020;167:155506.
28. Nogami S, Shida N, Iguchi S, et al. Mechanistic insights into the electrocatalytic hydrogenation of alkynes on Pt-Pd electrocatalysts in a proton-exchange membrane reactor. ACS Catal 2022;12:5430-40.
29. Fukazawa A, Shimizu Y, Shida N, Atobe M. Electrocatalytic hydrogenation of benzoic acids in a proton-exchange membrane reactor. Org Biomol Chem 2021;19:7363-8.
30. Mitsudo K, Inoue H, Niki Y, Sato E, Suga S. Electrochemical hydrogenation of enones using a proton-exchange membrane reactor: selectivity and utility. Beilstein J Org Chem 2022;18:1055-61.
31. Shimizu Y, Harada J, Fukazawa A, et al. Diastereoselective electrocatalytic hydrogenation of cyclic ketones using a proton-exchange membrane reactor: a step toward the electrification of fine-chemical production. ACS Energy Lett 2023;8:1010-7.
32. Nandenha J, Piasentin RM, Silva LMG, Fontes EH, Neto AO, de Souza RFB. Partial oxidation of methane and generation of electricity using a PEMFC. Ionics 2019;25:5077-82.
33. Coelho JF, Filho NGP, Gutierrez IM, et al. Methane-to-methanol conversion and power co-generation on palladium: nickel supported on antimony tin oxide catalysts in a polymeric electrolyte reactor-fuel cell (PER-FC). Res Chem Intermed 2022;48:5155-68.
34. Li W, Bonakdarpour A, Gyenge E, Wilkinson DP. Design of bifunctional electrodes for co-generation of electrical power and hydrogen peroxide. J Appl Electrochem 2018;48:985-93.
35. Yuan XZ, Ma ZF, Jiang QZ, Wu WS. Cogeneration of cyclohexylamine and electrical power using PEM fuel cell reactor. Electrochem Commun 2001;3:599-602.
36. Buzzo G, Rodrigues A, De Souza R, et al. Synthesis of hydroquinone with co-generation of electricity from phenol aqueous solution in a proton exchange membrane fuel cell reactor. Catal Commun 2015;59:113-5.
37. Ahmed S, Tao Z, Zhang H, et al. Review on chitosan and two-dimensional MoS2-based proton exchange membrane for fuel cell application: advances and perspectives. Energy Fuels 2023;37:1699-730.
38. Meyer Q, Yang C, Cheng Y, Zhao C. Overcoming the electrode challenges of high-temperature proton exchange membrane fuel cells. Electrochem Energy Rev 2023;6:16.
39. Cha JE, Cho WJ, Hwang J, Seo DJ, Choi YW, Kim WB. Fuel cell performance improvement via the steric effect of a hydrocarbon-based binder for cathode in proton exchange membrane fuel cells. Sci Rep 2022;12:14001.
40. Liu M, Hu H, Kong Y, et al. The role of ionomers in the electrolyte management of zero-gap MEA-based CO2 electrolysers: a Fumion vs. Nafion comparison. Appl Catal B Environ 2023;335:122885.
41. Wang L, Bevilacqua M, Chen YX, et al. Enhanced electro-oxidation of alcohols at electrochemically treated polycrystalline palladium surface. J Power Sources 2013;242:872-6.
42. Zaman S, Wang M, Liu H, et al. Carbon-based catalyst supports for oxygen reduction in proton-exchange membrane fuel cells. Trends Chem 2022;4:886-906.
43. Rodríguez-gómez A, Lepre E, Dorado F, Sanchez-silva L, Lopez-salas N, de la Osa AR. Efficient ethanol electro-reforming on bimetallic anodes supported on adenine-based noble carbons: hydrogen production and value-added chemicals. Mater Today Energy 2023;32:101231.
44. Zhao J, Liu H, Li X. Structure, property, and performance of catalyst layers in proton exchange membrane fuel cells. Electrochem Energ Rev 2023;6:13.
45. Rodríguez-gómez A, Dorado F, de Lucas-consuegra A, de la Osa AR. Influence of the GDL and assembly mode of a PEM cell on the ethanol revalorization into chemicals. Chem Eng J 2020;402:125298.
46. Yamanaka I, Onisawa T, Hashimoto T, Murayama T. A fuel-cell reactor for the direct synthesis of hydrogen peroxide alkaline solutions from H2 and O2. ChemSusChem 2011;4:494-501.
47. Oh LS, Han J, Lim E, Kim WB, Kim HJ. PtCu nanoparticle catalyst for electrocatalytic glycerol oxidation: how does the PtCu affect to glycerol oxidation reaction performance by changing pH conditions? Catalysts 2023;13:892.
Cite This Article
Export citation file: BibTeX | RIS
OAE Style
Jiang X, Chen R, Chen YX, Lu CZ. Proton exchange membrane fuel cells: application for value-added chemical productions. Chem Synth 2024;4:6. http://dx.doi.org/10.20517/cs.2023.44
AMA Style
Jiang X, Chen R, Chen YX, Lu CZ. Proton exchange membrane fuel cells: application for value-added chemical productions. Chemical Synthesis. 2024; 4(1): 6. http://dx.doi.org/10.20517/cs.2023.44
Chicago/Turabian Style
Jiang, Xia, Rui Chen, Yan-Xin Chen, Can-Zhong Lu. 2024. "Proton exchange membrane fuel cells: application for value-added chemical productions" Chemical Synthesis. 4, no.1: 6. http://dx.doi.org/10.20517/cs.2023.44
ACS Style
Jiang, X.; Chen R.; Chen Y.X.; Lu C.Z. Proton exchange membrane fuel cells: application for value-added chemical productions. Chem. Synth. 2024, 4, 6. http://dx.doi.org/10.20517/cs.2023.44
About This Article
Special Issue
Copyright
Data & Comments
Data
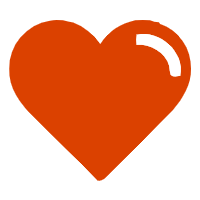

Comments
Comments must be written in English. Spam, offensive content, impersonation, and private information will not be permitted. If any comment is reported and identified as inappropriate content by OAE staff, the comment will be removed without notice. If you have any queries or need any help, please contact us at support@oaepublish.com.